In the demanding world of tobacco production, the efficiency and longevity of machinery is key to success – and ultimately, every machine is the sum of its parts, including those susceptible to wear and tear.
No matter how advanced an asset may be, it’s the individual components – especially those prone to attrition over time – that truly dictate its performance. These elements are the unsung heroes, ensuring that each asset functions optimally and meets the precise demands of tobacco manufacturing.
High-quality parts in tobacco machinery, particularly those replacing worn components, have a direct impact on production – and in turn, your business’ reputation, as well as financial performance.
So, it’s crucial to be familiar with the components that may experience normal wear and tear – and choose the right replacement when needed.
What is a ‘Wear and Tear’ Component?
A ‘wear and tear’ part in tobacco machinery refers to a component that is subject to gradual deterioration due to regular use in the manufacturing process. These parts are integral to the functioning of the machinery but are prone to damage, erosion, or breakdown over time because of constant operational stress.
In the context of tobacco machinery, this includes components that are repeatedly involved in high-speed, high-precision tasks – such as cutting, shaping, or packaging tobacco products.
These components are typically designed to be replaceable, as their eventual wear is inevitable due to the nature of their function in the manufacturing process. As a result, regular maintenance and timely replacement of these wear and tear parts is crucial to maintain the efficiency, productivity, and longevity of tobacco machinery.
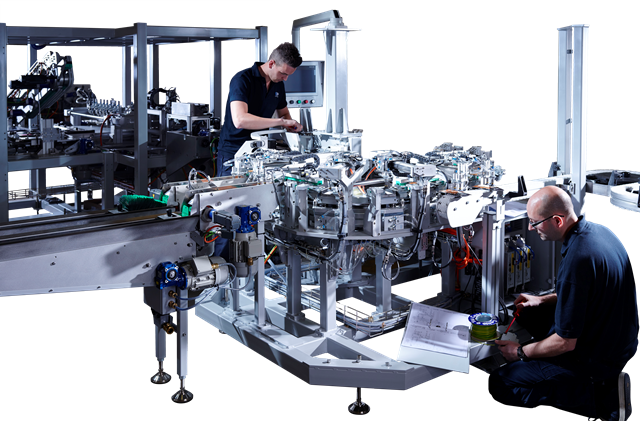
Common Wear and Tear Parts Explained
In Cigarette Making Machines:
- Knives, garniture tapes, dense end discs. These parts are crucial for the intricate processes of cigarette formation and are under constant stress.
- Bearings, belts, tobacco staves. Vital for movement and cutting actions.
- Tongue assemblies, suction belts, ecreteurs, drums. These components require timely assessments and replacements.
In Packing Machines:
- Gum Wheels. Essential for packaging integrity and used extensively, they must be of high quality to prevent product damage or waste.
Common to Both Processes:
- Sensors, Circuit Breakers, Replacement PLCs, Gears. Integral to automated processes, their failure can significantly disrupt production.
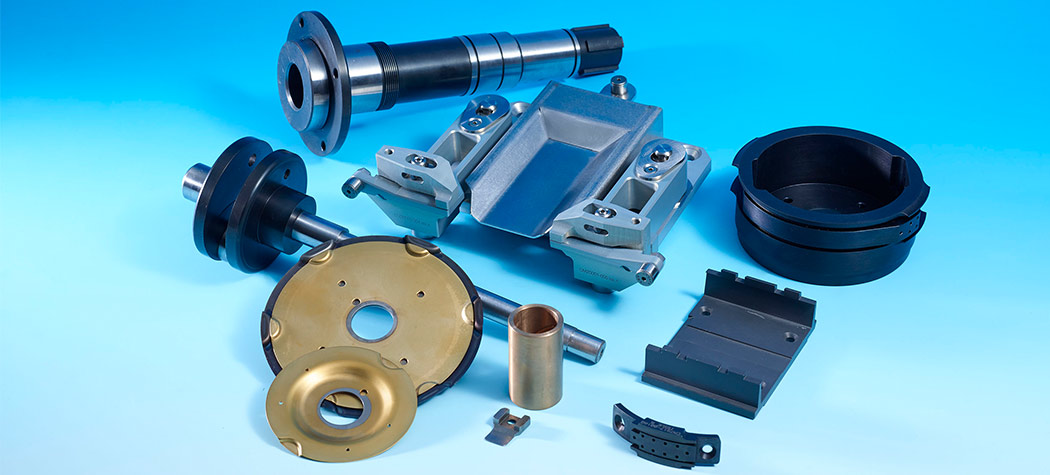
The Importance of Quality Parts
The resilience of machinery parts plays a critical role in combating wear and tear. Quality parts, designed for endurance, stand up to the relentless demands of constant operation, effectively reducing the need for frequent replacements.
When components like knives in cigarette makers or gum wheels in packing machines resist wear, the entire production line benefits from reduced downtime. This means more time is devoted to actual production rather than maintenance – a key factor in meeting stringent production deadlines.
Additionally, by minimising interruptions, quality parts enable smoother scaling of operations, ensuring that increased demand doesn’t lead to a proportional increase in machinery stress. The result is a more reliable production process, with a consistent output that meets both quality standards and market demands.
In essence, investing in quality parts is an investment in sustained productivity and reduced depletion of components, vital for the competitive tobacco industry.
Optimising Management of Wear and Tear Components to Minimise Downtime
To enhance the longevity and efficiency of tobacco machinery, it’s crucial to implement strategic management of wear and tear components. Here are five key approaches that can significantly reduce downtime and maintain consistent production quality:
- Regular Maintenance and Inspections. Establish a routine maintenance schedule and perform regular inspections to identify wear and tear early. This proactive approach allows for timely repairs or replacements, minimising downtime.
- Invest in Quality Replacement Parts. Prioritise high-quality replacement parts for longevity and better performance. Quality parts reduce the frequency of replacements, thereby saving costs in the long run.
- Effective Inventory Management. Maintain a well-organised inventory of essential wear and tear components. Having critical parts readily available can significantly reduce downtime during urgent replacements.
- Staff Training and Performance Monitoring. Train staff to recognise signs of wear and tear and utilise technology to monitor machinery performance. Early detection by knowledgeable staff and monitoring systems can prevent minor issues from becoming major breakdowns.
- Documentation and Supplier Relationships. Keep detailed records of all maintenance activities and develop strong relationships with reliable suppliers. Good record-keeping helps in tracking component lifecycles, and dependable suppliers ensure timely provision of high-quality parts.
By focusing on these areas, tobacco manufacturers can effectively manage wear and tear components, leading to enhanced machinery efficiency, reduced downtime, and overall improvement of production efficiency.
The CME Advantage
CME offers a robust solution as a centre point for all tobacco machine spare part needs.
Our versatility in supplying a wide array of OEM parts consolidates multiple sourcing processes into one operation, reducing complexity and costs. We even offer a dedicated stocking strategy, tailored to your usage patterns – ensuring essential spare parts are always available, thus minimising downtime and maximising efficiency.
Furthermore, CME provides technical support to navigate obsolescence challenges and offers data monitoring services for peak performance. By partnering with CME, you benefit from our commitment to the longevity and productivity of your machinery – ensuring seamless, efficient, and cost-effective tobacco processing operations.
KEEN TO ENHANCE YOUR TOBACCO MACHINERY EFFICIENCY? DISCOVER MORE HERE