As the legal cannabis market for both recreational and medical use continues to expand year on year within North America, and as the debate on the potential for increased use of cannabis products for medical purposes within the UK and Europe continues, the surge in demand for cannabis-based products has presented manufacturers with new challenges as they strive to achieve a significant increase in volume.
This article discusses the challenges faced by the legal cannabis sector as they scale up production levels to meet demand. The volume of product now being manufactured has also been the catalyst for the development of and investment in innovative automated systems to increase both output and quality.
The growth of the cannabis market in North America in recent years has been significant as increasing numbers of States legalise its use for medical and / or recreational purposes. Made illegal by the passing of an act as far back as 1937, in 1996 California was the first state to make cannabis legal for use in medical applications due to its effectiveness in managing a number of chronic conditions. Since then under the Cannabis Act in 2018, the Government of Canada legalised and strictly regulated the production, distribution, sale, import and export, and possession of cannabis for adults of legal age.
North America overall has been instrumental in the continued development and growth of this sector.
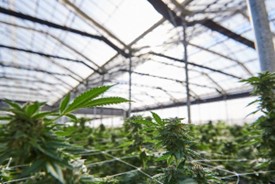
North America legal cannabis market growth
Statistics from a number of market sources indicate that the North America legal cannabis market size was valued at USD 12.4 billion in 2021 and is expected to rise steadily with a compound annual growth rate (CAGR) of 15.3% from 2022 to 2030. The overall demand is now such that the plants are being cultivated on an industrial scale in purpose-built greenhouses, some of which span millions of square feet.
Traditionally, this was an industry which was heavily reliant on manual operators to produce joints using low technology production aids. The increased demand and subsequent volume of production required has exacerbated the problems associated with manual production methods. Aside from the recruitment and retention issues, trying to achieve and maintain both consistent production and quality levels with increasing numbers of generally unskilled operators quickly becomes unsustainable. To overcome these challenges, many companies are embracing fully automated solutions that fill, weigh, compact, twist and package the finished products.
Automating Pre-Roll Production & Packing
One Multi State Manufacturer, within the USA, has made significant investments in a series of AutoCone machines, designed and built by UK based CME Limited. This sophisticated automation solution accepts delicate paper and card “cones” from an input magazine system before indexing them through various stations at the rate of up to 30 per minute, where product is dispensed to weight, compressed to a specified density, sealed by twist and trimmed before final weight verification. The system also achieves dispensing weigh control to a tolerance of +/- 10%. As one of the first of its kind in OEM production, careful consideration was given during the design process to the nuances associated with the previous manual production processes to guarantee reliable and efficient operation.
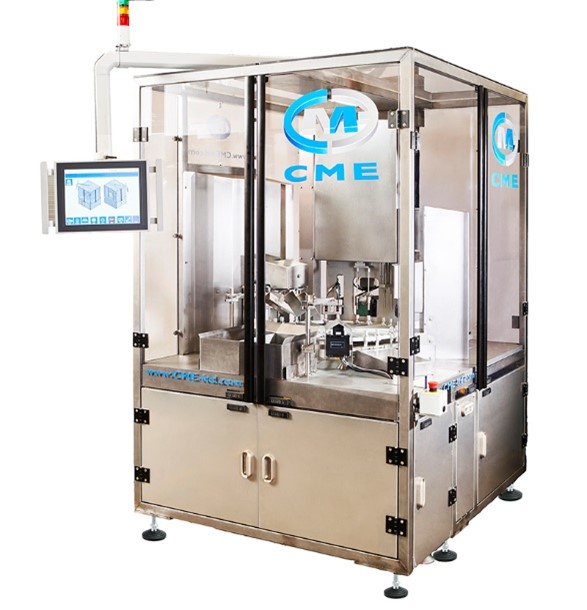
(CME’s AutoCone machine provides high volume product with consistent quality)
For example, manufacturers use multiple strains of product, which can differ in consistency and contain varying levels of moisture, therefore the coatings used on the product feeding surfaces are designed to maintain the required feed rate across all product grades.
Consistent cannabis joint twisting and sealing
Another example is the sealing / twisting process, which uses multiple servo-motors to consistently replicate the dexterity of the previous manual operation. The AutoCone machine is also designed ergonomically, and the man-machine interface is highly intuitive for ease of operation by production operatives.

(CME’s AutoCone machine uses multiple servo-motors to achieve consistent twisting / sealing on joints)
The performance from the AutoCone allowed the manufacturer in question to reduce headcount from 16 persons per shift to just 4. Production levels have now reached around 350,000 joints per month, with significant consistency and quality improvements, and the remaining personnel are now performing machine operation and tending duties.
A further benefit associated with the introduction of automation for manufacturers is the ability to re-train and upskill their personnel. In the case of the manufacturer mentioned here, one of their female operators was initially re-trained to run the company’s first AutoCone machine. Such was her enthusiasm for the technology, she has since been promoted to Director level and is now responsible for training operators in the use of automation within the company’s production facilities in other USA states.
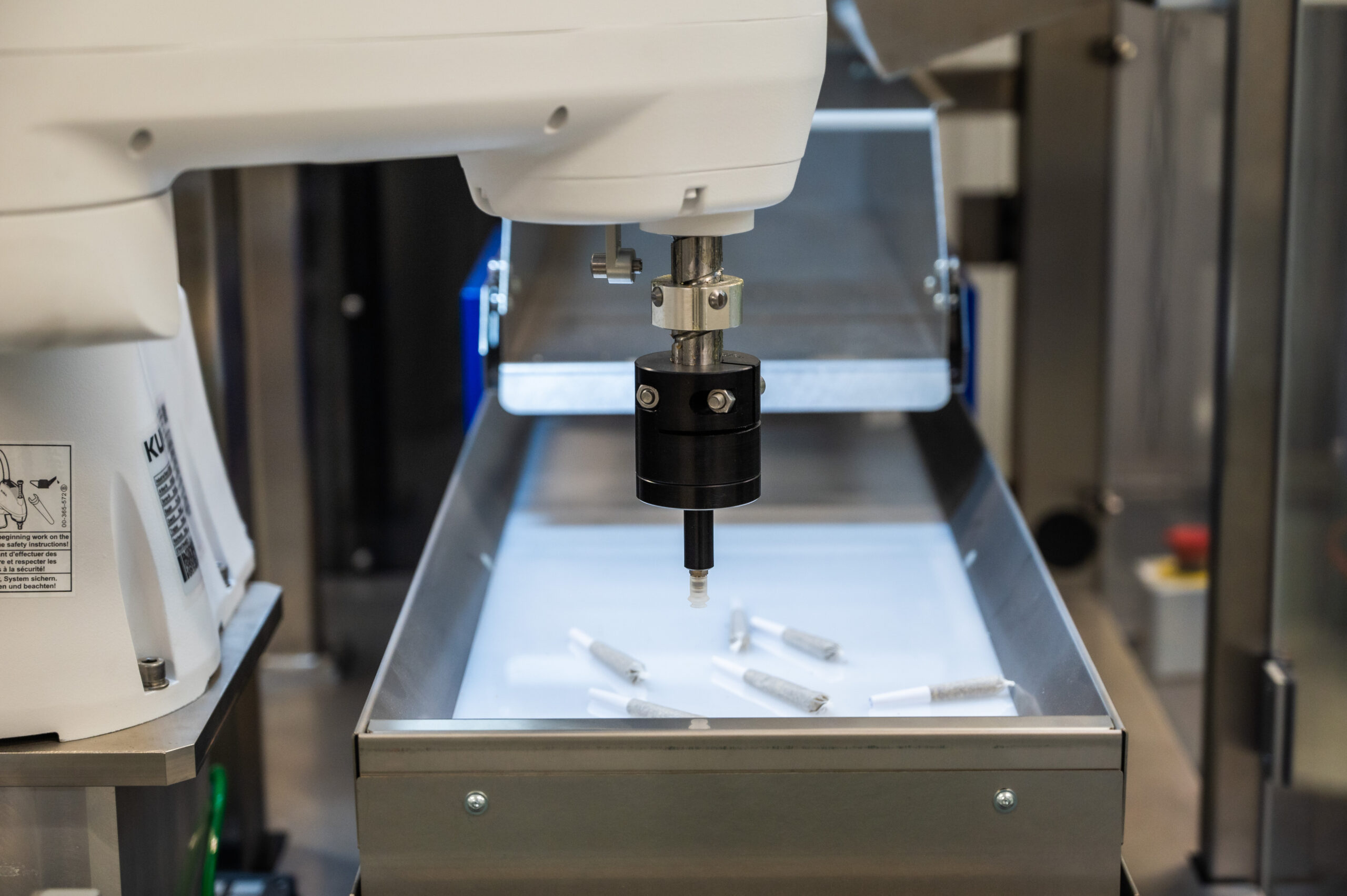
(CME’s Pre-Roll packaging system transfers finished product to trays)
A catalyst for further automation
The success of the automated technologies used to produce the pre-rolled joints was the catalyst for the introduction of further automated systems to perform the pre-roll packaging operations, and once again CME was at the forefront of the development of this technology
CME designed a flexible stand-alone system which picks pre-rolled cannabis products, presented in a random fashion on a vibratory feeding system. The products are then transferred and placed in a set configuration and orientation within a tray. This compact and cost-effective system can process up to 60 pre-rolls per minute with a vision system being used for product identification, position, and orientation, before a SCARA robot selects the product and transfers it to the packaging. Full sensor monitoring is also used for product quality and material supply. The system is designed to be quickly adjusted to operate across multiple packaging and product formats.
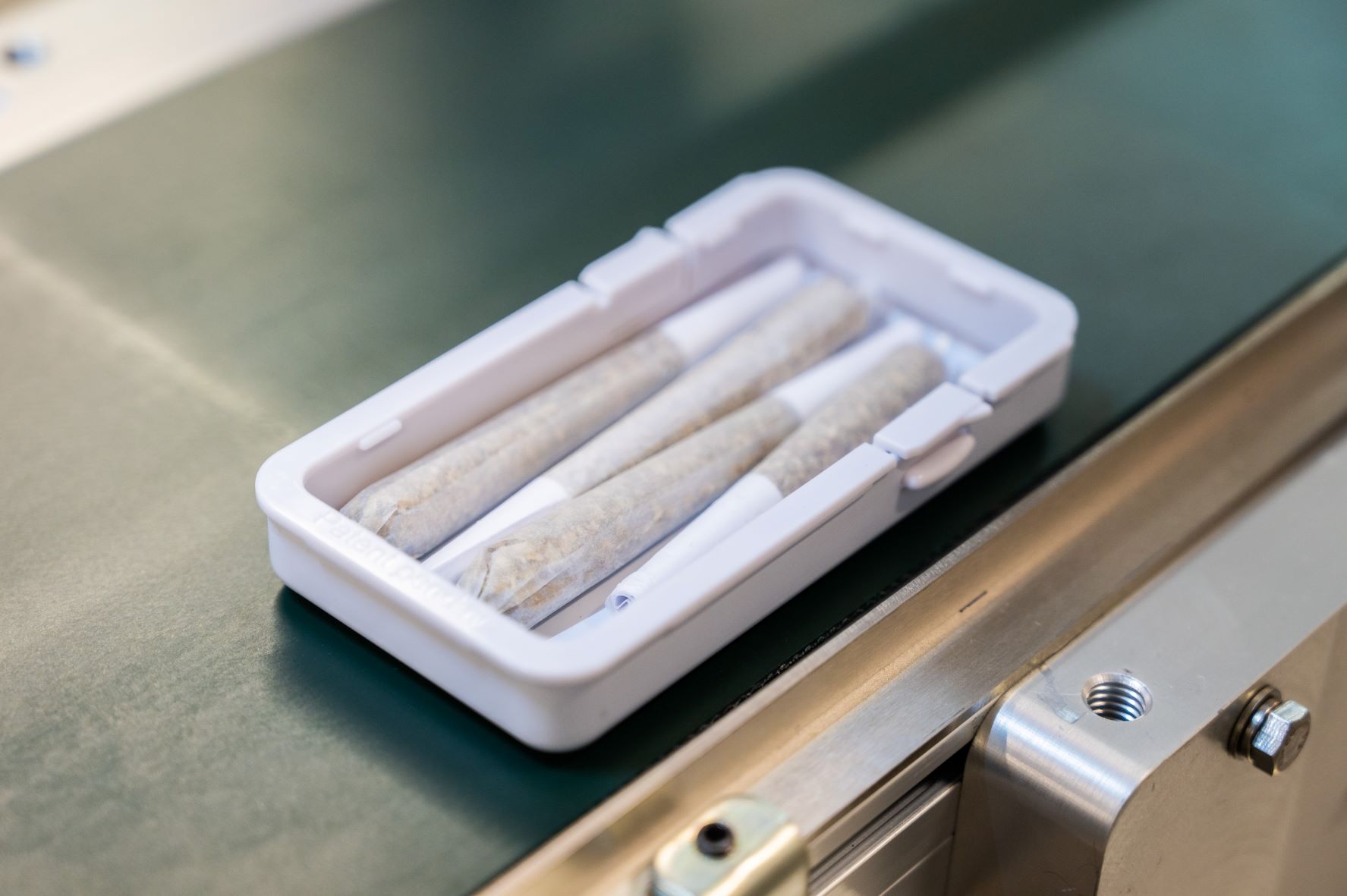
With the significant growth rate for the legal cannabis sector set to continue, at least until 2030, there is little doubt that volume manufacturers will continue to adopt the sector specific automation technologies that have to date been instrumental in helping them manage the transition from traditional highly labour-intensive production techniques to that of high-volume, high-quality automated production.