The Ultimate Guide to Tobacco Machine Spare Parts: Sourcing, Maintenance, and More
Your Comprehensive Resource for Enhancing Tobacco Machinery Efficiency.
Introduction to Tobacco Machine Spare Parts
The efficiency of tobacco production hinges on the reliability and performance of the machinery used in the process. Spare parts play a crucial role in this equation, determining not only the day-to-day functioning of tobacco machines but also their long-term viability.
In order to get the most from your machinery (and of course, the product it delivers) it’s important to pay close attention to the spares that keep it moving. Though they may be small, their impact is significant – so let’s dive in and discover precisely how to leverage spare parts to your businesses advantage.

Why Do Quality Spare Parts Matter for Tobacco Machinery?
The tobacco industry demands precision and dependability. Quality spare parts ensure that your tobacco machinery operates at peak performance, which is critical for maintaining production schedules (and protecting your reputation in the process).
There is a direct correlation between the quality of spare parts and the performance and longevity of machinery. You’ve probably heard the old adage of ‘buy cheap, buy twice’ – but in reality, when you’re working with a piece of machinery for many years, we’re not just talking about a couple of ad-hoc replacements. Poor quality parts can lead to countless hours of maintenance, damaging the overall lifespan (not to mention total cost of ownership) of the machines they have blighted.
In addition, the standard of the final tobacco product is often a reflection of the class of components used in production machinery. If machinery is fitted with second-rate parts, it can lead to host of undesirable product characteristics which then impact user experience.
Uneven cutting or shredding of tobacco, for example, can result in inconsistent burn rates and flavour. Additionally, faulty filters or packaging machinery can result in leaks, contamination, or damage to the tobacco product, undermining its quality and shelf life.
Unfortunately, the cost of substandard spare parts really does add up – even if your initial invoice seems favourable.
What Impact Do Quality Parts Have on Machinery Longevity?
Investing in quality spare parts is not just a matter of routine maintenance; it’s an investment in the machinery’s future.
High-grade components reduce the risk of unexpected failures that can cause costly downtime. With less wear and tear on critical components, equipment life is significantly extended, allowing for a more secure return on investment.
How Do Quality Parts Contribute to Efficiency and Reduced Downtime?
Quality parts are designed to last, which means they can withstand the rigors of constant use without frequent replacement. This durability translates into less time spent on repairs and more time spent in production. With increased uptime, tobacco machinery can meet the demands of tight production deadlines, enabling operations to scale efficiently with fewer interruptions.
Ultimately, unexpected downtime leads to significant production losses. Your labour costs will creep up as workers wait for machinery to be repaired, while you urgently seek out replacement parts (often at high cost, due to lack of scope to negotiate). This unexpected break in production also disrupts the supply chain, resulting in delayed orders and decreased customer satisfaction – harming both your company’s reputation and financial performance.
By understanding more about the spares you buy – as well as weighing up performance vs. price – you can make the crucial decisions that positively affect your bottom line.
What Are Common Wear and Tear Components of Tobacco Machines?
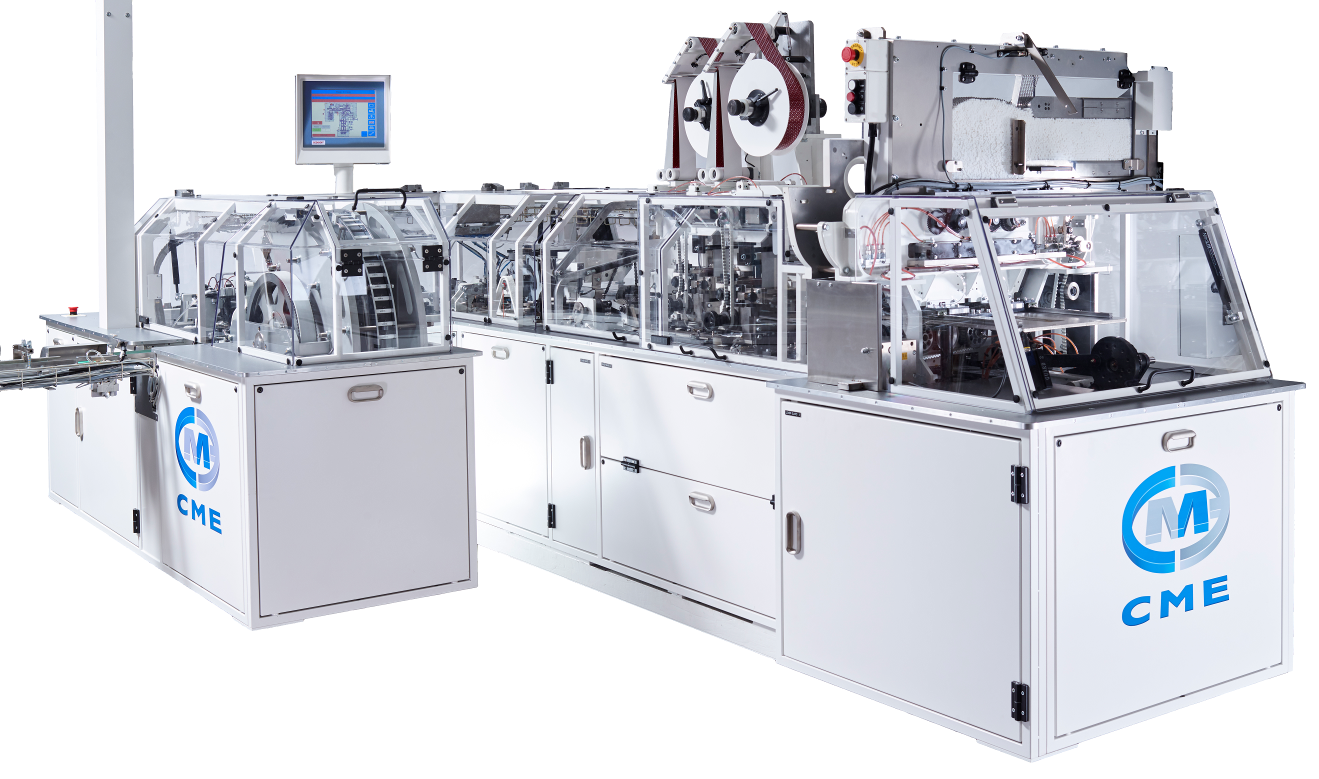
Both cigarette making and packing machines have specific components that are prone to regular wear and tear.
For cigarette makers, frequent movement and cutting actions involve parts like:
- Knives
- Garniture tapes
- Dense end discs
- Bearings
- Belts
- Tobacco staves
- Tongue assemblies
- Suction belts
- Ecreteurs
- Drums.
These components are vital for the intricate processes of cigarette formation and are constantly under stress, requiring timely assessments and replacements.
In the case of packing machines, components such as gum wheels are essential for packaging integrity and are used extensively. The quality of these wheels must be high to ensure that packaging processes do not falter, leading to potential product damage or waste.
Both making and packaging processes rely on the smooth functioning of:
- Sensors
- Circuit breakers
- Replacement PLCs (Programmable Logic Controllers)
- Gears.
All of these parts are integral to the automated processes of modern tobacco machinery, and their failure can lead to significant disruption in production. It’s vital, therefore, to purchase the most suitable components to suit your process.
In the following sections, we’ll provide a more detailed look at sourcing strategies, maintenance tips and the latest in tobacco machine spare part technology – so you’re fully equipped to streamline your operations for better productivity and efficiency.
How to Source and Select the Right Spare Parts for Your Tobacco Machinery
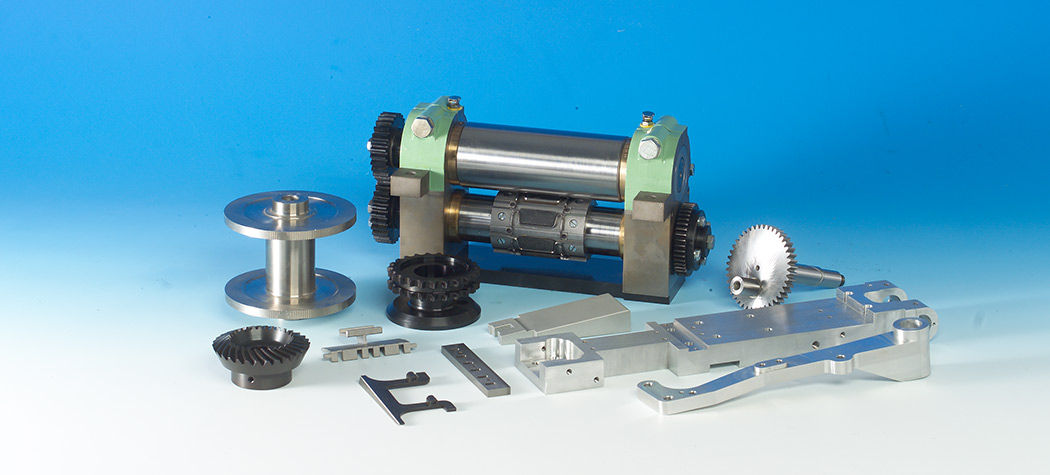
When it comes to creating optimum efficiency on your production line, sourcing and selecting the right parts for your tobacco machinery is essential.
This isn’t just a part that fits, or ‘does the job’. Let’s discuss what it really means to choose the right components – as well as how to establish a relationship with the right supplier, who can deliver true value through the best quality and service.
Tips for Choosing the Right Spare Parts
When the time comes to purchase new parts for your tobacco machinery, being well-informed is critical.
Here’s some tips to help…
- Consult the Machinery Manual. It’s the most direct way to identify the exact part number and specifications required for your equipment.
- Check Part Markings. Most spare parts come with a part number marked on them. This identification helps in verifying that the parts are genuine and suitable for your machinery.
- Select a Knowledgeable Provider. Partner with suppliers like CME who aren’t just vendors but experts in your specific machinery. They should provide support and advice, not just a sale.
- Prioritise Quality Over Price. While budget considerations are of course important, cheap alternatives can cost more in the long run due to premature failure and potential damage to your machinery.
How Do I Ensure Compatibility and Quality in Spare Parts Selection?
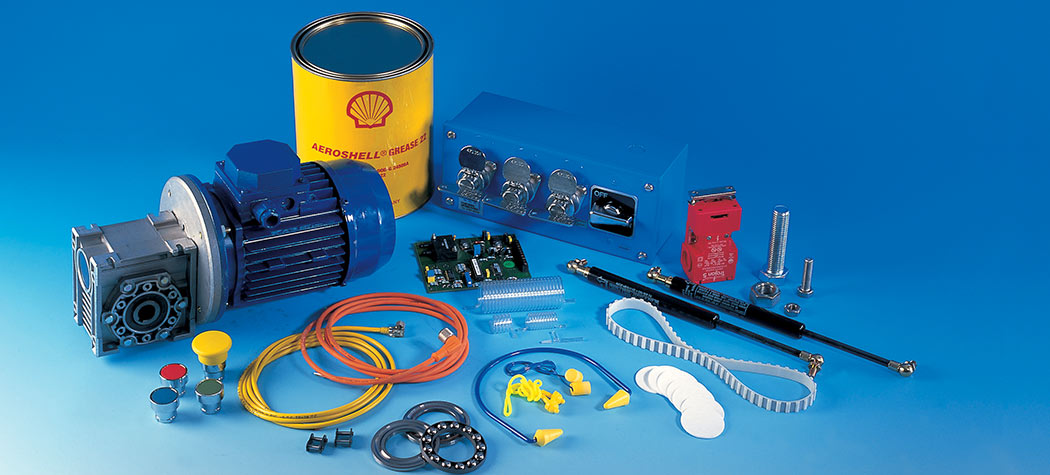
We’ve discussed the importance of quality at length – but how can you guarantee it?
Ultimately, quality assurance comes from choosing reputable suppliers who attest that their parts will fit and function as intended, on the first try. High-quality materials, precise heat treatment, and appropriate surface finishing techniques are all indicators of a superior part.
When it comes to compatibility, matching the part number and referring to detailed machinery information – like the manual – will ensure that the new parts fit and function correctly with existing systems.
Assessing functionality post-fitting is also a good barometer for quality. Evaluate how well the part performs once installed, including its durability and ability to fulfil the job required. If it deteriorates quickly or hinders production output, you’ll know that the component isn’t up to standard.
Maximise Your Tobacco Production Efficiency!
Discover tailored solutions that fit your specific machinery needs. Connect with our experts today on our Inquiry Page for personalised advice and superior spare part options to elevate your production line.
What Should I Look for in Supplier Reputation and Reliability?
When selecting a supplier for your spare parts, consider the following factors to gauge their reputation and reliability.
- Industry Tenure. Look at how long the supplier has been in business. Longevity can indicate stability, experience, and a proven track record.
- Expertise and Knowledge. A supplier with comprehensive knowledge of tobacco machinery will offer invaluable support. Suppliers should understand the intricacies of the equipment they sell parts for, as opposed to those who may simply reverse engineer parts without an in-depth understanding of their application.
- Quality of Service. Assess the level of service provided by the supplier, including their responsiveness, warranty offerings, and after-sales support.
Selecting the right tobacco machinery spare parts is a balance of thorough research, knowledge application, and choosing partners who are committed to the quality and longevity of their products.
Next, we’ll delve into the all-important practice of preventative maintenance – and precisely how your spare parts can help.
Preventative Maintenance with Tobacco Machine Spare Parts
Preventative maintenance is an essential practice that keeps tobacco machinery in peak condition, maximises uptime, and ensures consistent output quality. This proactive approach to maintenance not only optimises production but also helps in managing operational costs and resources more effectively.
Why is Preventative Maintenance Important for My Tobacco Machinery?
The objective of preventative maintenance is to foresee and prevent machine failures before they occur.
Scheduled maintenance allows for:
- Maximised Uptime. Regular checks and replacements of wear components ensure machines run with minimal unexpected breakdowns, sustaining productivity.
- Spread of Operational Costs. Scheduled maintenance allows for the distribution of expenses over time, avoiding the sudden financial impact associated with major repairs.
- Resource Planning. Scheduling maintenance ensures that resources – including both parts, and labour – are available when needed, without disrupting the production process.
By incorporating a preventative maintenance strategy, tobacco companies can plan downtime for maintenance, aligning it with production schedules and budgetary constraints.
How to Implement Preventative Maintenance Practices
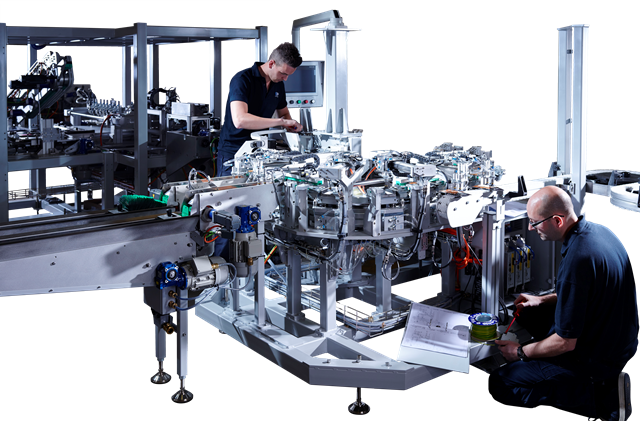
A robust preventative maintenance program considers several factors, which include:
- Operational Hours Tracking. Monitor the number of hours the machinery operates to determine maintenance schedules based on manufacturer recommendations.
- Forecasting Output Needs. Anticipate your production needs to avoid maintenance during peak production periods.
- Considering the Age of Equipment. Older machinery may require more frequent checks and part replacements compared to newer equipment.
- Coordinated Scheduling. Whenever possible, align maintenance tasks for multiple machines to occur simultaneously to minimise the impact on operations.
- Timely Ordering of Spare Parts. Based on the maintenance schedule, order spare parts well in advance to prevent delays. Maintain a stock of critical components to ensure they are available when required.
Implementing these practices will require a detailed understanding of your machinery’s needs and careful planning to ensure that maintenance activities are seamlessly integrated into your operations.
By following a preventative maintenance schedule and keeping a well-organised inventory of spare parts, you can significantly extend the life of your machinery and enhance overall efficiency.
What Solutions Can Extend Tobacco Machinery Lifespan?
Maximising the lifespan of tobacco machinery not only increases productivity but also enhances the return on investment for tobacco manufacturing facilities. This section explores various strategies and solutions that can be implemented to tackle obsolescence, design improvements, and sub-assembly exchange services to keep machines running longer and more reliably.
Removing Obsolescence Challenges
Overcoming the challenges of obsolete machinery requires a multi-faceted approach…
- Comprehensive Maintenance. Regular and thorough maintenance schedules ensure that each part of the machinery is functioning correctly and efficiently. This attention prevents small issues from turning into larger problems that can shorten the life of the machine.
- Proactive Preventative Maintenance. Preventative maintenance includes servicing equipment before failures occur and planning for parts replacement that is prone to wear and tear.
- Upgrading Electrical Systems. Modernising the electrical components of tobacco machinery, such as control systems and drives, can enhance performance, efficiency, and compatibility with new technologies.
- Component Improvement. Regularly upgrading components to the latest standards can improve both the machinery’s longevity and the quality of output, adapting to the latest industry demands.
- Supplier Relationships. Keeping in close contact with spare part suppliers ensures that you stay ahead of potential obsolescence. Outsourcing maintenance to a trusted provider who can offer regular updates and improvements is another strategy to consider.
Design Improvements for Longevity
Continual design enhancements are vital for extending machinery life. These improvements can be as simple as using wear-resistant materials for high-stress parts or as complex as redesigning a component to reduce stress on the machine.
Engaging with manufacturers for recommended upgrades can keep machinery up to date with the latest design protocols and materials.
Sub-Assembly Exchange Services for Continuous Operation
Sub-assembly exchange programs are an excellent way to minimise downtime.
This service involves exchanging whole sub-assemblies that are worn or due for maintenance with refurbished or new ones, allowing machines to continue operating while maintenance is performed off-site. These services ensure that there is always a functioning part in place, facilitating a continuous operation and reducing stops in production.
By integrating these solutions into regular maintenance schedules, tobacco manufacturers can significantly extend the operational life of their machinery. It allows for a consistent production process, lowers long-term costs, and enhances overall efficiency.
Next, we’ll take a look at the role spare parts play in machinery upgrades and how this can improve performance on your production line.
Tobacco Machinery Upgrades: Enhancing Performance with Spare Parts
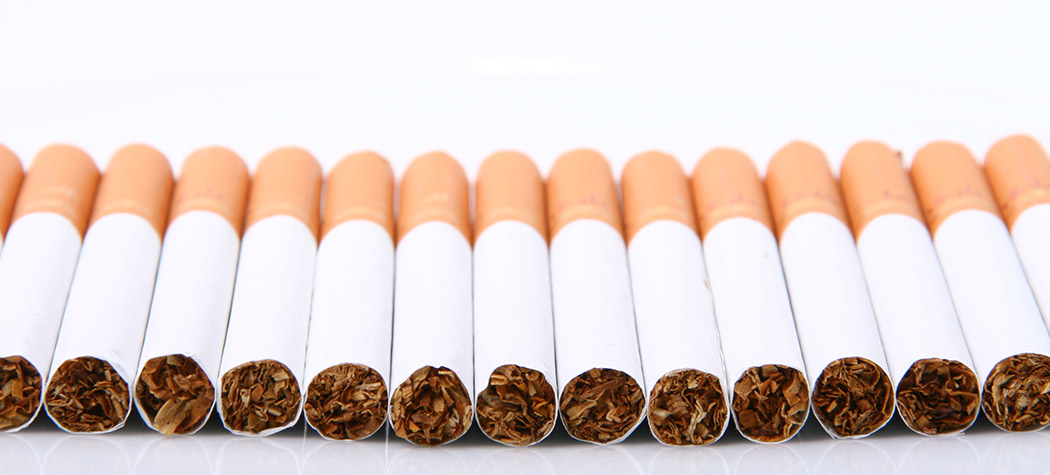
Upgrading tobacco machinery is a strategic initiative to keep pace with evolving industry trends, regulatory demands, and technological advancements. By selecting the right spare parts, companies can enhance performance, overcome obsolescence, and stay competitive.
Adapting to Industry Trends and Regulations
The tobacco industry is subject to stringent regulations that can change rapidly, requiring adaptable production processes. Upgrades can help ensure compliance with new laws, such as those related to product safety and environmental standards. For instance, introducing parts that reduce waste or improve the filtration process can both improve the sustainability of operations and align with new regulatory requirements.
Overcoming Tobacco Machinery Obsolescence
Machinery obsolescence is a significant challenge, especially in an industry with a long history like tobacco production. Upgrades through spare parts can transform an outdated system into a modernised workhorse, ready to deliver quality products. This process might include replacing mechanical controls with digital ones, improving cutting systems, or introducing more durable and efficient motors and drives.
Can Specific Spare Parts Improve Tobacco Machinery Performance?
Absolutely! Strategic replacement of specific spare parts can significantly enhance how machines perform. Here are some ways that spare parts can be used to upgrade tobacco machinery…
- Material Improvements. This involves utilising parts made from advanced materials that resist wear and tear better than their conventional counterparts. For example, replacing standard knives in cigarette makers with ones made from newer alloys can provide a sharper, longer-lasting cut, leading to less downtime and maintenance.
- Design Improvements. Spare parts with updated designs can directly address the limitations of older models. A redesigned suction belt, for instance, might offer better grip and speed, resulting in improved feed rates and less product waste.
- Efficiency Enhancements. Newer part designs can also contribute to energy efficiency. By fitting machinery with optimised gears and bearings, manufacturers can reduce power consumption, which cuts operational costs and supports a greener production protocol.
- Output Quality. Upgraded parts can refine the precision of machinery operations, thus improving the consistency and quality of the tobacco product. For example, new-generation garniture tapes might offer better tension control, translating to cigarettes with consistent packing and appearance.
Your choice and integration of specific high-quality spare parts is critical for keeping tobacco machinery in line with current demands and futureproofing it against market and regulatory changes. By selecting upgrades carefully, manufacturers can ensure their machinery remains reliable, efficient, and capable of producing a product that meets the highest standards of quality and compliance.
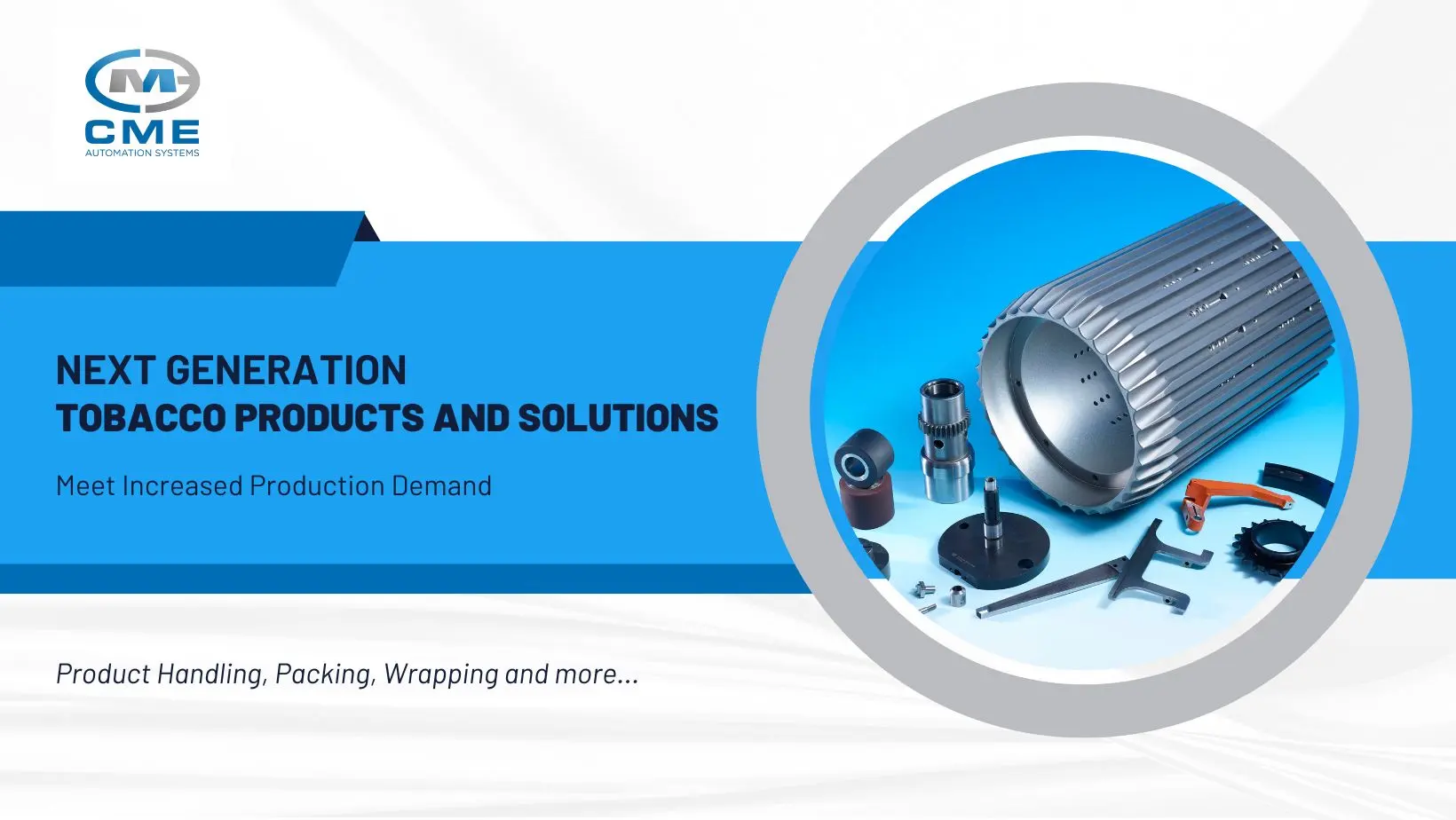
Main Tobacco Machine Types
The tobacco industry leverages a variety of specialist machinery for different stages of cigarette production and packaging. Understanding the main types of machines and their functions is crucial for operators to maintain efficiency and keep production running smoothly.
Machine Categories in Tobacco Production
- Primary Processing Equipment. This equipment handles the initial stages of tobacco processing, preparing the raw material for cigarette production.
- Secondary processing equipment. This refers to machines that process intermediate tobacco products into final forms.
- Makers. These machines are involved in the actual production of cigarettes, creating the finished rods from tobacco blends.
- Packers. Packers are responsible for packaging cigarettes into boxes, ensuring they are ready for distribution.
- Reclaimers. Reclaimers are used to recover tobacco from defective products so the material can be reused.
- Tax Stampers. Tax stamping is a legal requirement in many regions, with machines designed to apply tax stamps to packets accurately and efficiently.
- Wrappers. Wrapper machines apply the outer wrapping to cigarette packs, often the final touch before boxing for shipment.
Next, we’ll explore the specific functions and operating principles of each machine type in detail, providing a deep dive into how they fit into the tobacco production process – as well as how the efficiency and longevity can be maximised through proper maintenance.
What Are the Key Components and Accessories in Tobacco Machines?
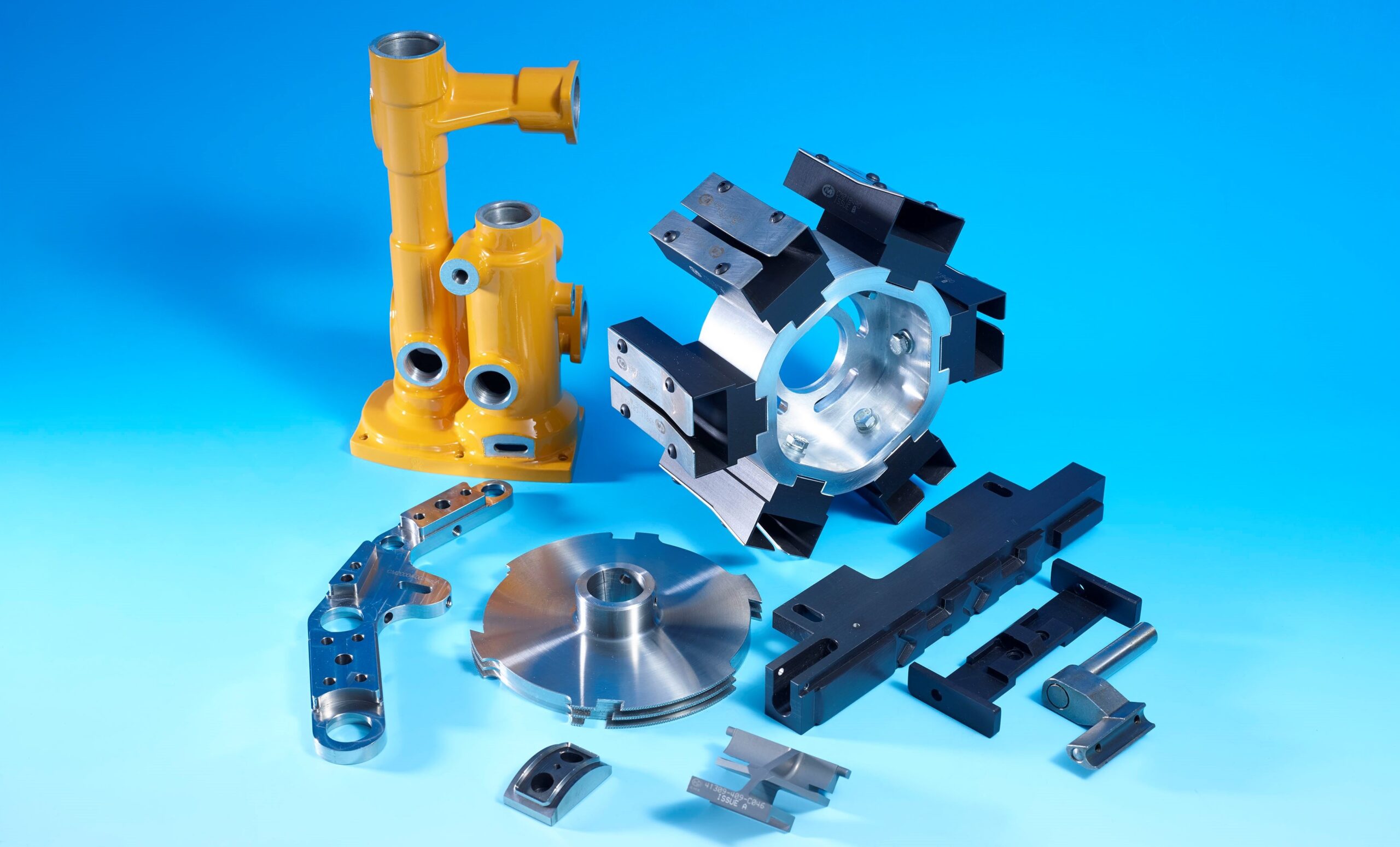
In tobacco machines, you are likely to find…
- Garniture Tape. This is a critical component in cigarette making machines, where it helps to shape and wrap the cigarette paper around the tobacco column.
- Suction Tape. Suction tape is used in cigarette making machines to transport the tobacco, by providing a vacuum grip through its perforations. This ensures a steady flow during production.
- Loose End Detectors. These are sensors used to check that the ends of cigarettes are properly filled with tobacco, supporting quality control by detecting any loosely packed ends that may compromise the product’s integrity.
- U Knives. U Knives are specialised cutting tools, often involved in the cutting or shaping of tobacco leaves or the final product.
- Dense End Discs. Dense end discs are used to compact tobacco at the ends of a cigarette, ensuring a tight pack and preventing the tobacco from falling out.
- Tobacco Machine Pockets. In the context of cigarette packing machines, pockets are mechanical components that hold and transfer cigarette packs or cartons during the packaging process, ensuring that they are in the correct orientation for further processing.
Transitioning from the essential roles played by the various components and accessories within tobacco machines, it’s important to consider the flexibility these machines offer in product variation. This adaptability is largely enabled by packing format change kits, which allow manufacturers to alter pack sizes and cigarette dimensions with ease.
Ready to Enhance Your Tobacco Production?
For custom solutions and expert advice on your tobacco machinery needs, visit our Enquiry Page. Let’s discuss how we can optimise your operations with our high-quality spare parts and dedicated support.
What Are Packing Format Change Kits?
Packing format change kits are integral to the cigarette manufacturing process, providing the necessary parts to convert packaging machinery to accommodate different pack sizes or cigarette dimensions. They are a crucial element for manufacturers who need to switch between product variations without investing in entirely new machinery.
How Do Cigarette Packing Format Change Kits Work?
A change kit consists of a series of replaceable modules or parts that can be installed in existing cigarette packing machines.
These kits typically include various guides, drums, trays, and other components that can be easily swapped out to reconfigure the machine for different packet sizes or cigarette lengths. The reconfiguration allows the machine to adapt to new packaging standards, such as different graphic health warnings or pack dimensions required by law or market demand.
What Packet Quantities Are Available in Cigarette Pack Kits?
The range of packet quantities that can be achieved with format cigarette format change kits is diverse, allowing manufacturers to produce standard packs of 20 cigarettes, smaller packs of 10, or any other commercially relevant quantity.
The kits also enable the machinery to adjust to various cigarette sizes, like king-size or super slims, ensuring that the packing process remains efficient and versatile regardless of the product specifications.
With these kits, tobacco companies can remain agile, adjusting their production lines to shifting market trends, consumer preferences, and regulatory requirements without significant downtime or capital expenditure on new packing lines. This makes change kits an essential part of maintaining a responsive and flexible manufacturing operation.
As we’ve discussed the adaptability offered by packing format change kits, it’s equally crucial to address the maintenance aspect that ensures the smooth functioning of tobacco machinery. Maintenance kits are the unsung heroes in this scenario, equipping manufacturers with the tools and parts needed for routine upkeep and proactive care.
Tobacco Machine Maintenance Kits
What Are Maintenance Kits?
Maintenance kits are pre-assembled packages containing all the necessary parts for scheduled service intervals of tobacco machinery, such as after every 5000 hours of operation. They’re custom-tailored to address wear and tear that affects machine performance over time.
Why Are Maintenance Kits Important?
These kits play a vital role in preventing unscheduled downtime by replacing worn components before they fail. Regular maintenance is essential for avoiding costly emergency stops and maintaining consistent production quality.
What Are the Components of a Comprehensive Maintenance Kit?
A comprehensive maintenance kit typically includes a variety of parts that are known to exhibit wear over time, like belts, chains, bearings, springs, pawls, rollers, bushes, gears, pins, clutches, and rails. Sensors may also be included, as they are vital for machine operation and often require calibration or replacement to ensure accuracy and functionality.
What Are the Benefits for Overall Machinery Care?
The use of maintenance kits can result in more predictable and planned machinery management, optimising uptime and ensuring that the quality of output remains high.
By investing in regular maintenance, tobacco manufacturers can also better forecast their operational costs and schedule maintenance work to minimise impact on production.
In essence, maintenance kits not only preserve the health and longevity of tobacco machinery but also anchor the efficiency and reliability of the entire manufacturing process, ensuring that the operations can continue to meet demand without interruption.
Progressing from the vital role of maintenance kits in pre-emptive tobacco machinery care, efficient management of spare parts inventory emerges as another cornerstone of operational excellence. Proper inventory data cleansing can streamline spare parts management, directly impacting a facility’s performance and cost-efficiency.
Inventory Data Cleansing: Efficient Spare Parts Management
What Are the Most Common Challenges in Managing Tobacco Spare Parts Inventory?
The challenges in managing a tobacco spare parts inventory are multifaceted, including determining the optimal stock levels for various components, minimising capital locked in unused stock, and timing re-order points to guarantee availability without overstocking. These complexities are compounded when handling parts for machines from different OEMs, each with unique lead times and costs.
How Can I Optimise My Inventory Data for Better Management?
Optimising inventory data involves regular analysis of part usage, factoring in operational hours, maintenance schedules, and historical consumption patterns. By forecasting needs accurately, companies can keep inventory lean while accounting for potential delays due to shipping or customs issues. Efficient management may also include divesting stagnant stock through sales or transfers between facilities.
What Inventory Strategies Can Help Reduce Operating Costs?
Strategies to reduce inventory costs include partnering with reputable aftermarket suppliers for quality parts at lower prices, investing in long-life design improvements to extend replacement intervals, and implementing dedicated or consignment stock arrangements for critical components.
Consolidating purchases with fewer suppliers to leverage volume discounts, reduce administrative tasks, and decrease shipping and customs fees can further streamline inventory management.
By keeping these strategies in mind, tobacco manufacturers can maintain a balanced approach to inventory management—keeping the necessary parts on hand while minimising financial and operational inefficiencies. The result is a spare parts system that supports continuous operation and sustains high productivity without unnecessary financial burden.
Building on the streamlined approach to managing spare parts inventory, we now delve into another pragmatic aspect of maintenance – repairing subassemblies, which can be a cost-efficient alternative to whole machine overhauls or replacements.
Repairing Subassemblies: Cost-Efficient Machinery Maintenance
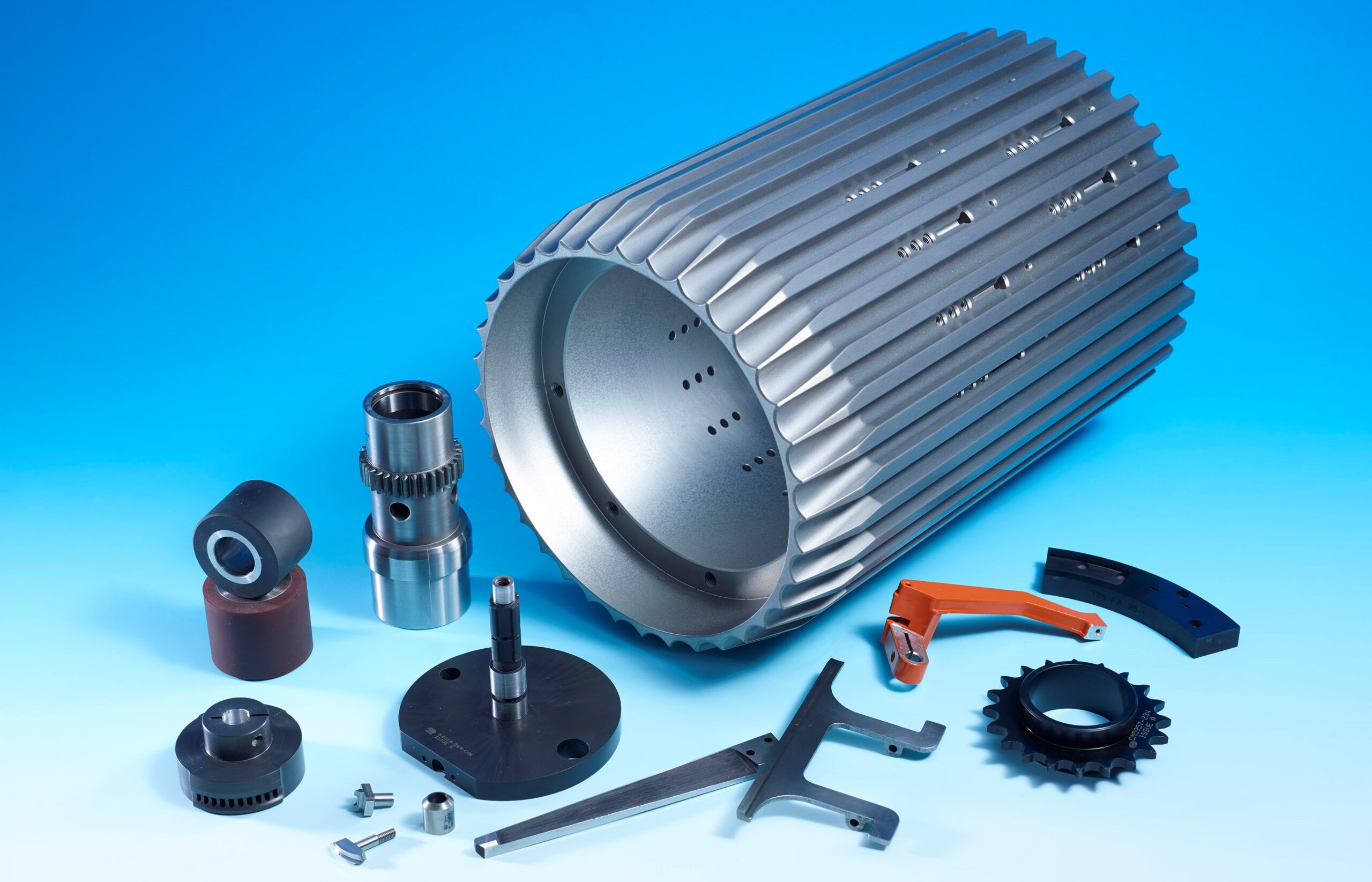
What Are the Benefits of Subassembly Repairs?
Repairing subassemblies offers a multitude of benefits, such as faster replacement times that translate to increased machinery uptime and throughput. By fixing or replacing smaller components or subassemblies, technicians can address specific issues without dismantling entire machines, leading to more focused and less disruptive maintenance.
What Tools and Training Are Necessary for Subassembly Repairs?
Effective subassembly repairs require specialist tools that align with the technical specifications of the tobacco machinery.
Technicians must be proficient in using these tools and have a deep understanding of the machinery’s operations to perform precise and reliable repairs. Additionally, proper training is essential to ensure that maintenance staff can diagnose issues accurately and carry out repairs that adhere to quality and safety standards. This often means investing in ongoing education and certification programs to keep skills current with the evolving complexities of tobacco machinery technology.
By focusing on subassembly repairs, tobacco manufacturing facilities can not only reduce maintenance costs but also enhance the overall efficiency of their machinery, ensuring a consistent output of high-quality products.
After exploring the efficiencies of subassembly repairs for tobacco machinery maintenance, another innovative strategy for optimal spare parts management comes into play: stock consignment. This procurement solution offers streamlined processes and cost savings, which can significantly bolster a company’s operational agility.
How Can Stock Consignment Streamline the Spare Parts Procurement Process?
What Is the Concept Behind Consignment Stock?
Consignment stock is an agreement where a supplier places a stock of parts at a client’s facility, retaining ownership until the parts are used.
This model ensures immediate availability of essential spare parts on-site, which a facility can access and use as needed. Billing occurs only upon usage, after which the supplier replenishes the stock, creating a cycle of continuous supply.
How Does It Simplify Procurement?
Stock consignment simplifies procurement by reducing the number of purchase orders raised and ensuring parts are available right when they’re needed, effectively eliminating the usual ordering process. This system minimises procurement steps and focuses on a reliable replenishment process, thereby saving time and administrative effort.
Reducing Lead Times and Costs
By having consignment stock, the time typically associated with lead times is virtually eliminated, directly increasing machinery uptime. Financially, it translates to cost savings by shrinking the need for emergency orders and express shipping.
Additionally, the risk of machine downtime due to parts failure is significantly reduced, as parts can be replaced proactively based on wear, not just upon failure.
What Are the Advantages for Part Availability?
The consignment model offers unparalleled part availability, crucial for maintaining continuous production. This on-site presence of parts ensures that maintenance and repairs can be carried out instantly, without waiting for part delivery. For the supplier, this model provides a predictable demand for stock replenishment and enables better inventory planning and control.
In sum, consignment stock is a win-win for both tobacco machinery operators and spare parts suppliers, fostering a partnership that promotes efficiency and cost-effectiveness. By embracing this approach, companies can achieve a more resilient and responsive supply chain, essential for meeting the high demands of tobacco production.
Moving from the convenience of on-site spare parts availability through stock consignment, we next turn our attention to how tobacco machinery performance can be further enhanced through innovative support services. Remote technical support represents a paradigm shift in maintaining high-efficiency levels and ensuring the uninterrupted operation of tobacco machinery.
Remote Technical Support: Enhancing Machinery Performance
What Role Does Remote Troubleshooting and Support Play in Machinery Performance?
Remote technical support allows for immediate troubleshooting and problem-solving without the need for an on-site visit from a technician.
This is crucial in maintaining continuous machine performance, as experts can guide operators through diagnostics and repairs in real-time, using advanced communication tools and monitoring systems.
What Are the Benefits of Remote Assistance for Smooth Machinery Operations?
Remote assistance brings a multitude of benefits, including:
- Expert Availability. Access to the best experts who understand the intricacies of tobacco machinery, regardless of geographical location.
- Cost-Effectiveness. Eliminates travel and associated costs for on-site service visits, directly impacting the bottom line by lowering operational expenses.
- Proactive Issue Resolution. Enables the detection of potential problems before they escalate into more serious failures, thus preserving machine integrity.
- Operational Efficiency. Ensures machines run optimally, with minimal disruptions to production schedules.
- Data-Driven Decisions. Utilisation of operational data to make informed decisions on maintenance and performance, leading to a more strategic approach to machine upkeep.
By integrating remote support into their maintenance strategy, tobacco manufacturers can enjoy reduced downtime, access to immediate assistance, and the continuous, optimal performance of their machinery, all while controlling costs and benefiting from expert guidance.
When it comes to enhancing tobacco machinery efficiency, it’s clear that having the right partner for sourcing spare parts and maintaining your machinery is vital.
CME offers a robust solution, serving as a one-stop shop for all your tobacco machine spare parts needs.
Our versatility in supplying a wide array of OEM parts consolidates multiple sourcing processes into one streamlined operation, reducing the complexity and costs associated with managing separate orders, freight, and invoices.
Beyond simplifying the procurement process, CME’s dedicated stocking strategy is tailored to your specific usage patterns, ensuring that the essential spare parts are always at hand when you need them. This proactive approach minimises downtime and maximises efficiency, enabling you to maintain continuous production flow.
Furthermore, CME’s customer service extends to technical support, helping you navigate the challenges of obsolescence, and offering data monitoring services that keep your tobacco machinery operating at peak performance.
By partnering with CME, you benefit from their commitment to your machinery’s longevity and productivity, ensuring that your tobacco processing operations are seamless, efficient, and cost-effective.